WHY USE HOISTING?
Our skilled national hoist team is ready to support you in planning, configuring and supplying hoists to meet all your lifting needs, both above and below ground.
We are proud to offer you the largest construction hoist fleet of personnel and materials hoists in Europe, so whether you need support in a solution to build the next Shard or are assessing project plans to go safely underground we're here to help.
With over 600 hoists in our fleet and hundreds of innovative solutions available we are guaranteed to be able to devise the perfect solution for your precise needs. Why not get in touch to talk through your project with our experts?
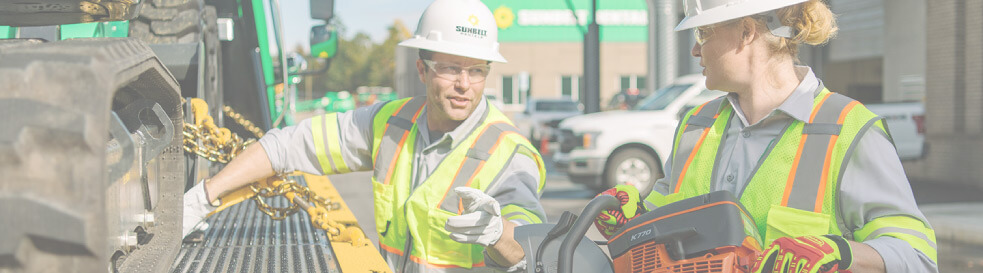
Our Full Service Cycle
Accessories
To enable our standard hoist cages and industrial lifts to be configured for maximum safety and efficiency, Sunbelt Rentals offers a range of accessories that are available for most hoists. These include:
Landing Protection Panels – The panels are fitted either side of the landing gate to prevent site staff from touching the hoist cage as it travels past – or stops at – the landing. These are secured to the hoist vertical pipe superstructure and are fitted during the hoist installation.
Landing Infill Plates – Infill plates are installed to bridge the gap between the hoist superstructure and the site landings. The use of landing infill plates also restricts the gap between the hoist cage floor edge and landing edge to below 50mm as required by BS7212.
Foundation Steel Plates – Designed to avoid the necessity to fix the hoist base assembly down to concrete floors, or where the hoist is placed on a soft surface. GB Access can supply a steel plate to go under the hoist base which is bolted down to the plate. The standard F S P plate size is 4000 x 2500 x 40mm and weighs 3200Kg, which is sufficient to absorb the upwards forces in the event of a hoist striking the bottom buffers.
Landing Bridges – Where the hoist is mounted away from the building or scaffolding landing edge, we can supply and install a landing bridge. This will provide a safe walkway between the hoist cage and landing. The landing bridges are equipped with protection panels at the hoist end and full length handrails and toeboards to minimise the risk of items falling from the bridge.
Landing bridges are the same width as the hoist cage and available in lengths up to 6.0 metres.
Top Hats – These are available to be fitted to the roof of passenger goods hoists over the cage roof trapdoor. This allows the safe transportation of long items within the cage / top hat, without the possibility of the load falling from the hoist cage.
Pipe Carriers – These can be fitted to goods only hoists and enable scaffold poles etc. to be carried safely.
Design & Engineering
TEXT AND IMAGE TO FOLLOW – use ‘lorem’ for now for text and blank holding space for image
Delivery
Delivery of our rental hoists is typically made by one of our rigid lorries fitted with a Palfinger lorry mounted crane, equipped with lifting accessories and driven by a trained driver / operator.
All deliveries of our hoist equipment to site are planned in advance to ensure minimum site disruption and inconvenience. Our delivery fleet of 8 wheel construction chassis vehicles can self-offload and position the hoist base assembly at up to 12 metres of the vehicle, depending on site conditions.
Our FORS registered HGV fleet is Crossrail compliant and fitted with the latest emissions controls, allowing them to carry out deliveries anywhere in the UK.
Some of our larger hoist cage / base assemblies exceed 2.9 metres width and travel as ‘Abnormal Loads’. When this is required, Sunbelt Rentals registers the Abnormal Load movement and travel in accordance to the requirements of the movement order. Within the Metropolitan Police area these restrict the movement times of the vehicle and, in these instances, sites are advised of the early delivery time to ensure that the site is open to receive the delivery.
Deliveries are met by Sunbelt Rentals installation engineers and supervisors to guide the vehicle to the correct location and position the hoist according to prepared installation drawings, following the site indicated grid lines, where available.
Toolbox talks are carried out with the hiab operator and installation engineers to ensure that all members of the team understand what is required and all safety matters are explained so the necessary control measures are in place prior to offloading and placing the delivery.
All mast sections, superstructure and ancillary items are offloaded adjacent to the installation site to minimise manual handling during the installation.
Where site tower cranes are available to place the hoist away from the access roads or for all slipform hoist installations, our installation engineers will liaise with the site banksman to ensure that the hoist equipment is slung correctly and placed according to the installation drawings and site preparation.
Testing
Testing of all hoist installations is required under LOLER regulations following installation, at regular intervals (six months for passenger / goods hoists and 12 months for goods only and beam hoists) or following modification. These tests are undertaken by a Sunbelt Rentals qualified Thorough Examiner.
Carrying out a thorough examination of the hoist following installation, partial dismantle, modification or significant mechanical damage is required under LOLER regulations.
A visual inspection is made of the complete installation by a competent person trained to carry out the thorough examination, who will also check the integrity of all connections on the mast, superstructure and ties before carrying out a load test.
This consists of loading the hoist with 125% of its Safe Working Load and driving the hoist up its full length of travel, stopping the cage near to the tie points to check both the structural integrity of the mast and superstructure as well as the holding ability of the drive motor brakes.
When the hoist receives its routine test (at six monthly intervals for passenger goods hoists or 12 monthly intervals for goods only hoists) the load test is carried out with the hoist SWL weight only.
Following a satisfactory load test, the hoist manufacturer’s patented safety device is drop tested with the Safe Working Load of the hoist. This is designed to bring the descent of the hoist to a controlled stop within 2 metres, if the descent speed is greater than 125% of normal, ensuring the safety of the occupants.
Following the load and drop test, the structure is inspected again to ensure that there has been no deterioration from the tests and that all aspects of the hoist operate correctly before Sunbelt Rentals issues a Report of Thorough Examination.
video
Lorem ipsum dolor sit amet, consectetur adipiscing elit, sed do eiusmod tempor incididunt ut labore et dolore . Ut enim ad minim veniam, quis nostrud exercitation ullamco laboris nisi ut aliquip ex ea commodo consequat. Duis aute irure dolor in reprehenderit in voluptate velit esse cillum dolore eu fugiat nulla pariatur. Excepteur sint occaecat cupidatat non proident, sunt in culpa qui officia.
To enable our standard hoist cages and industrial lifts to be configured for maximum safety and efficiency, Sunbelt Rentals offers a range of accessories that are available for most hoists. These include:
Landing Protection Panels – The panels are fitted either side of the landing gate to prevent site staff from touching the hoist cage as it travels past – or stops at – the landing. These are secured to the hoist vertical pipe superstructure and are fitted during the hoist installation.
Landing Infill Plates – Infill plates are installed to bridge the gap between the hoist superstructure and the site landings. The use of landing infill plates also restricts the gap between the hoist cage floor edge and landing edge to below 50mm as required by BS7212.
Foundation Steel Plates – Designed to avoid the necessity to fix the hoist base assembly down to concrete floors, or where the hoist is placed on a soft surface. GB Access can supply a steel plate to go under the hoist base which is bolted down to the plate. The standard F S P plate size is 4000 x 2500 x 40mm and weighs 3200Kg, which is sufficient to absorb the upwards forces in the event of a hoist striking the bottom buffers.
Landing Bridges – Where the hoist is mounted away from the building or scaffolding landing edge, we can supply and install a landing bridge. This will provide a safe walkway between the hoist cage and landing. The landing bridges are equipped with protection panels at the hoist end and full length handrails and toeboards to minimise the risk of items falling from the bridge.
Landing bridges are the same width as the hoist cage and available in lengths up to 6.0 metres.
Top Hats – These are available to be fitted to the roof of passenger goods hoists over the cage roof trapdoor. This allows the safe transportation of long items within the cage / top hat, without the possibility of the load falling from the hoist cage.
Pipe Carriers – These can be fitted to goods only hoists and enable scaffold poles etc. to be carried safely.
TEXT AND IMAGE TO FOLLOW – use ‘lorem’ for now for text and blank holding space for image
Delivery of our rental hoists is typically made by one of our rigid lorries fitted with a Palfinger lorry mounted crane, equipped with lifting accessories and driven by a trained driver / operator.
All deliveries of our hoist equipment to site are planned in advance to ensure minimum site disruption and inconvenience. Our delivery fleet of 8 wheel construction chassis vehicles can self-offload and position the hoist base assembly at up to 12 metres of the vehicle, depending on site conditions.
Our FORS registered HGV fleet is Crossrail compliant and fitted with the latest emissions controls, allowing them to carry out deliveries anywhere in the UK.
Some of our larger hoist cage / base assemblies exceed 2.9 metres width and travel as ‘Abnormal Loads’. When this is required, Sunbelt Rentals registers the Abnormal Load movement and travel in accordance to the requirements of the movement order. Within the Metropolitan Police area these restrict the movement times of the vehicle and, in these instances, sites are advised of the early delivery time to ensure that the site is open to receive the delivery.
Deliveries are met by Sunbelt Rentals installation engineers and supervisors to guide the vehicle to the correct location and position the hoist according to prepared installation drawings, following the site indicated grid lines, where available.
Toolbox talks are carried out with the hiab operator and installation engineers to ensure that all members of the team understand what is required and all safety matters are explained so the necessary control measures are in place prior to offloading and placing the delivery.
All mast sections, superstructure and ancillary items are offloaded adjacent to the installation site to minimise manual handling during the installation.
Where site tower cranes are available to place the hoist away from the access roads or for all slipform hoist installations, our installation engineers will liaise with the site banksman to ensure that the hoist equipment is slung correctly and placed according to the installation drawings and site preparation.
Testing of all hoist installations is required under LOLER regulations following installation, at regular intervals (six months for passenger / goods hoists and 12 months for goods only and beam hoists) or following modification. These tests are undertaken by a Sunbelt Rentals qualified Thorough Examiner.
Carrying out a thorough examination of the hoist following installation, partial dismantle, modification or significant mechanical damage is required under LOLER regulations.
A visual inspection is made of the complete installation by a competent person trained to carry out the thorough examination, who will also check the integrity of all connections on the mast, superstructure and ties before carrying out a load test.
This consists of loading the hoist with 125% of its Safe Working Load and driving the hoist up its full length of travel, stopping the cage near to the tie points to check both the structural integrity of the mast and superstructure as well as the holding ability of the drive motor brakes.
When the hoist receives its routine test (at six monthly intervals for passenger goods hoists or 12 monthly intervals for goods only hoists) the load test is carried out with the hoist SWL weight only.
Following a satisfactory load test, the hoist manufacturer’s patented safety device is drop tested with the Safe Working Load of the hoist. This is designed to bring the descent of the hoist to a controlled stop within 2 metres, if the descent speed is greater than 125% of normal, ensuring the safety of the occupants.
Following the load and drop test, the structure is inspected again to ensure that there has been no deterioration from the tests and that all aspects of the hoist operate correctly before Sunbelt Rentals issues a Report of Thorough Examination.
Lorem ipsum dolor sit amet, consectetur adipiscing elit, sed do eiusmod tempor incididunt ut labore et dolore . Ut enim ad minim veniam, quis nostrud exercitation ullamco laboris nisi ut aliquip ex ea commodo consequat. Duis aute irure dolor in reprehenderit in voluptate velit esse cillum dolore eu fugiat nulla pariatur. Excepteur sint occaecat cupidatat non proident, sunt in culpa qui officia.
Case Studies
For all enquiries please talk to our specialist team: Wigan: 01942 716 706, hoists@sunbeltrentals.co.uk Peterborough: 01832 272 408, hire@gbaccess.co.uk